
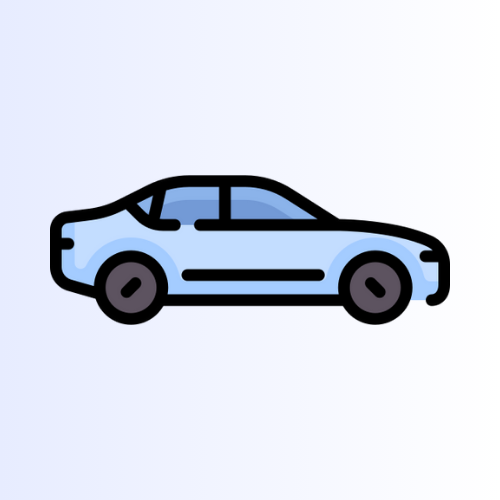
Your fear is burning your truck down because of the breaker auto-resetting and causing a program, right? Adding a fuse before the breaker will allow the breaker to operate normally. But if it’s a serious problem, like an actual short and not a temporary overcurrent, the fuse will blow and not reset.
DineR